匣钵的生产制造过程是由原材料粉末体,由液压机向模具施加一定压力,实现快速模压成型。匣钵成型液压机采用上、下油缸双向压制的结构,使得压制的匣钵强度高,密度均匀,焙烧后不开裂;可根据更换不同的模具来压制各种规格的匣钵制品。根据匣钵的材质、规格尺寸,选用不同吨位的液压机,常用有500吨、630吨、800吨、1000吨、1200吨、1500吨等四梁四柱液压机,山东威力重工多种吨位都可设计定做。这里我们以1000吨匣钵成型液压机为例,简单介绍下,匣钵双向压制的过程是怎样的?
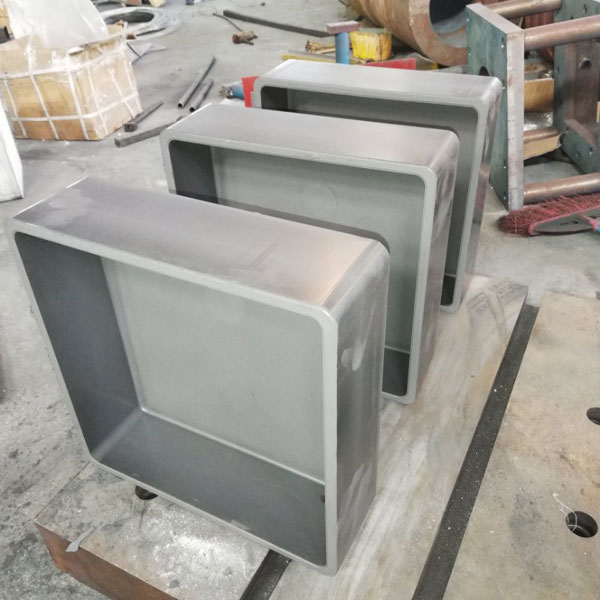
干压成型匣钵
1000吨匣钵成型液压机双向压制过程如下:
1、1000吨匣钵成型液压机原始工作状态上,主油缸上行到位,下油缸退回到位,布料箱退回到位,将按钮调整到全自动工作模式;按启动按钮,下油缸慢速上行,带动下压头和模框慢速向上移动,这时凹模开口处与下压头顶部形成一定空间;送料油缸开始布料,通过导轨运行至凹模上部;触碰到行程开关后停止,经多次连续抖动布料后,模具内已布满原材料;布料油缸自动退回到原始位置,碰到送料停止行程开关后停下来;主油缸带动滑块和上冲头快速下行,触碰到下行程开关后,上压头缓慢压制。
2、1000吨匣钵成型液压机在压制时需要设定排气次数和保压时间,压制过程中达到调定压力时开始延时保压,保压时间到主油缸自动回程,碰到行程开关停止上行,同时下油缸的开始下行退回,带动下压头和模框向下移动一定距离停止;成型坯体露出完成脱模,一个成型过程就完成了,重复上述动作实现全自动生产。
匣钵压制成型方法:
将匣钵粉料按照预设高度布料在模框,底部下模芯和侧部下模形成的模腔中,底部下模芯和侧部下模将位于其上方的匣钵粉料分为底部粉料集合体和侧边粉料集合体,上模芯向所述模腔压下,底部下模芯保持不动,侧部下模向上顶起,通过上模芯,底部下模芯和侧部下模的相对运动压制形成匣钵;压制过程中,底部粉料集合体和侧边粉料集合体的压缩比保持相同。
1000吨匣钵成型液压机机身设计采用四梁四柱式结构,配有伺服数控系统,机器的强度、刚度和精度保持性较好,通过油缸和滑块下行,模具不动的方式实现双面加压的成型工艺,使设备的能量效率更加显著,成型压力高,可靠,保证了匣钵的密度和强度,全自动制作设备自动化程度高、生产周期短、产量高。机器的上、下滑梁和立柱通过紧固螺母固定,调整螺母可调整主机精度。
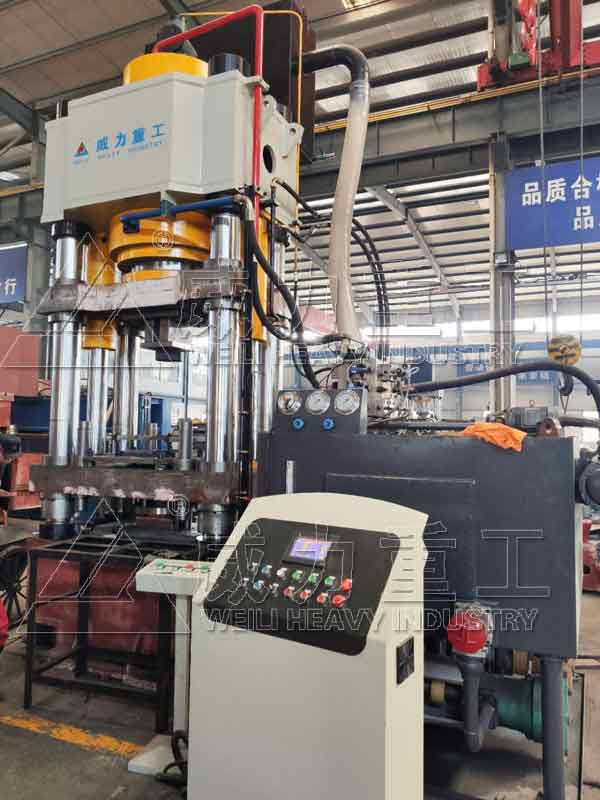
1000吨四梁四柱液压机
1000吨匣钵成型液压机的优势:
1、型号齐全,吨位从300-1200吨都有,可满足不同客户对产量的需求;
2、四梁四柱结构,定位精确,不会出现压偏、压坏模具现象,产品成品率高,外观整齐美观;
3、1000吨匣钵成型液压机采用先进液压传动系统,稳定性强,运行平稳,无噪音,大大提高了设备使用寿命;
4、采用PLC可编程控制器,可实现全自动压制,自动上料、自动布料、自动压制、自动出产品,降低了劳动强度,提高生产效率;
5、采用独特双面加压生产工艺,匣钵上下压力一致,强度均匀;
6、设备能设置排气时间,不会出现裂缝和裂层现象,可根据原材料的不同设置不同排气时间;
7、一台1000吨匣钵成型液压机可生产多种规格的匣钵(标型及其它异型匣钵),只要更换模具即可,根据模具方便快捷。
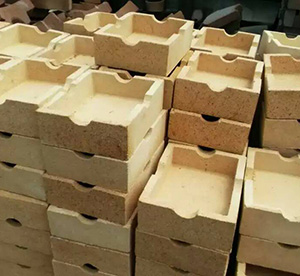
耐火材料匣钵
上一篇:上一篇:630吨粒子钢压块机生产制造如火如荼进行中
下一篇:下一篇:1200吨四柱液压机冲压成型汽车配件的工作原理